Troubleshooting Common Issues When Working with Non-Woven Interlining
- stkinterliningseme
- May 30, 2023
- 6 min read
Updated: Sep 12, 2023
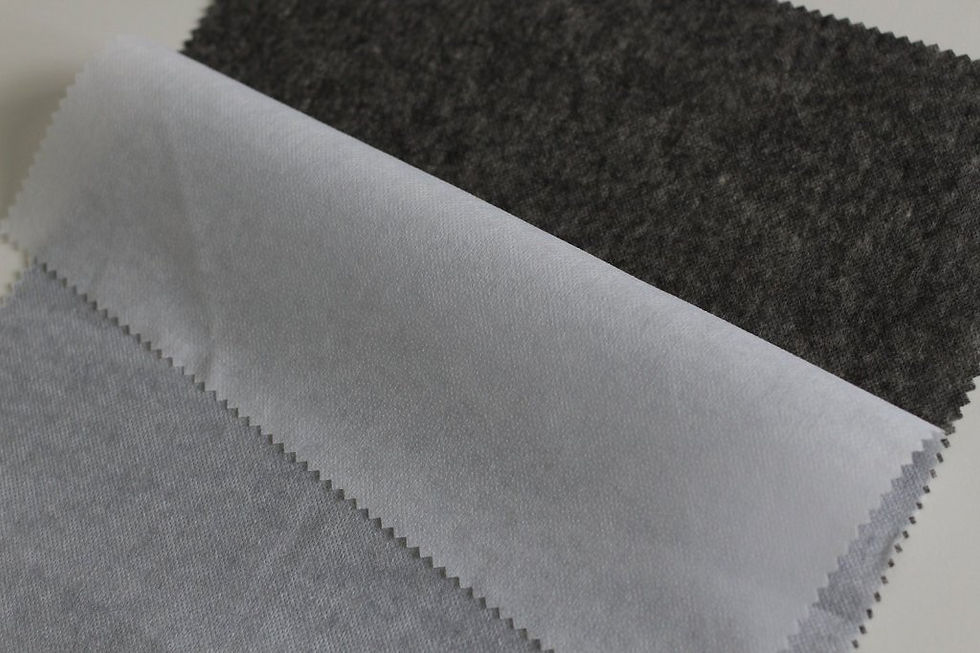
Non-woven interlining has become an essential material in the garment industry, offering stability, structure, and shape to various types of fabrics. However, like any other material, Non Woven Interlining can present its fair share of challenges during garment construction. In this blog post, we will explore some of the most common issues when working with non-woven interlining and provide troubleshooting tips to help you overcome them effectively.
1. Adhesive Failure Non-woven interlining relies on adhesives to adhere to fabrics, providing support and reinforcement. Adhesive failure can occur for various reasons, such as improper application, poor quality adhesive, or incorrect bonding temperature. This section will discuss troubleshooting adhesive failure issues, including tips on selecting the right adhesive, applying it correctly, and ensuring proper bonding temperatures.
2. Shrinkage and Stretching Shrinkage and stretching can be frustrating problems when working with non-woven interlining. These issues can lead to distorted garment shapes, uneven finishes, and compromised durability. This section will delve into the causes of Shrinkage and stretching and provide troubleshooting techniques such as pre-shrinking the interlining, using appropriate ironing techniques, and considering fabric compatibility to prevent or minimize these problems.
3. Wrinkling and Creasing Wrinkling and creasing are common issues that can occur during the sewing and pressing stages. These problems can result in an unprofessional appearance and affect the overall quality of the finished garment. This section will explore various factors contributing to wrinkling and creasing, such as excessive tension, incorrect pressing techniques, and inadequate interlining support. Troubleshooting tips will include proper handling and storing interlining, using suitable pressing tools, and adjusting sewing techniques to mitigate these issues effectively.
4. Delamination Means separating layers within the non-woven interlining, compromising its integrity and performance. Factors like excessive heat, incorrect washing methods, and low-quality interlining can contribute to Delamination. This section will address the causes of Delamination and provide troubleshooting strategies, such as using interlinings with better adhesive properties, following proper care instructions, and avoiding extreme temperature conditions.
5. Compatibility with Different Fabrics Non-woven interlining may not always be compatible with every fabric type, leading to issues like stiffness, puckering, or an unnatural drape. Understanding fabric compatibility is crucial for achieving the desired results. This section will explore different fabric characteristics and discuss how to troubleshoot compatibility issues, including selecting appropriate interlining weights, testing samples before the final application, and considering alternative interlining manufacturers.
Words Working with Non-Woven Interlining
Non-woven interlining has revolutionized the garment industry, offering various benefits such as stability, structure, and shape retention. Whether you are a seasoned professional or a beginner, understanding the intricacies of working with non-woven interlining is essential to achieve optimal results in garment construction. This comprehensive guide will explore the various aspects of working with non woven interlining Fabric, including its types, application techniques, tips for success, and troubleshooting common issues.
Understanding Non-Woven Interlining
Non-woven interlining is a vital component in garment construction, providing support, structure, and shape retention to various types of fabrics. It is a versatile material that has gained popularity in the textile industry due to its unique characteristics and benefits. This section will explore the concept of non-woven interlining, its composition, its advantages, and its wide applications.
1. What is Non-Woven Interlining? Non-woven interlining is a type of fabric that is manufactured without a traditional weaving process. Unlike woven fabrics created by interlacing yarns, non-woven fabrics are produced by bonding or felting fibers together using mechanical, thermal, or chemical methods. This bonding technique creates a stable, layered structure with unique properties suitable for interlining applications.
2. Composition of Non-Woven Interlining Non-woven interlining is typically composed of synthetic fibers such as polyester or polyamide. These fibers are chosen for their durability, stability, and compatibility with different types of fabrics. The fibers are processed using specialized machinery to create a web-like structure, bonded to form the interlining material. Additional elements, such as adhesive coatings or special finishes, may enhance performance depending on the desired characteristics.
3. Advantages of Non-Woven Interlining Non-woven interlining offers several advantages that make it a preferred choice for garment construction.
Stability and Structure
Non-woven interlining provides fabric stability and structure, enhancing their drape and shape retention. It adds body and support to lightweight or flimsy fabrics, making them easier to handle during sewing and ensuring a professional finish.
Reinforcement: By adding non-woven interlining to certain areas of a garment, such as collars, cuffs, or waistbands, you can reinforce those sections, increasing their durability and preventing sagging or distortion over time.
Fusibility: Many non-woven interlinings are fusible, meaning they have an adhesive coating that can be activated with heat. This allows for easy and secure attachment to the fabric, eliminating the need for extensive hand-sewing.
Versatility: Non-woven interlining is available in various weights and stiffness levels, allowing you to choose the most suitable option for different garment styles and fabric types. It can be used in light and heavy-weight fabrics, making it adaptable to different fashion designs.
Applications of Non-Woven Interlining Non-woven interlining finds extensive use in garment construction, particularly in the following areas:
Collars and Cuffs: Interlining provides shape and stability to collars and cuffs, giving them a crisp and well-defined appearance.
Waistbands: Non-woven interlining reinforces waistbands, ensuring they maintain their shape and support.
Button Plackets: Interlining adds structure and strength to button plackets, preventing them from puckering or stretching.
Hems and Facings: By incorporating non-woven interlining in hems and facings, you can achieve clean and professional finishes with improved durability.
Structured Garments: Non-woven interlining is widely used in tailored garments, such as suits and jackets, to create structure and provide shape retention.
Non-woven interlining is a valuable material in the garment industry, offering stability, reinforcement, and structure to various fabrics. Understanding its composition, advantages, and applications is crucial for achieving optimal results in garment construction. By incorporating non-woven interlining effectively, you can enhance your garments' overall quality and longevity, ensuring a polished and professional finish
Application Techniques Preparing the Interlining and Fabric
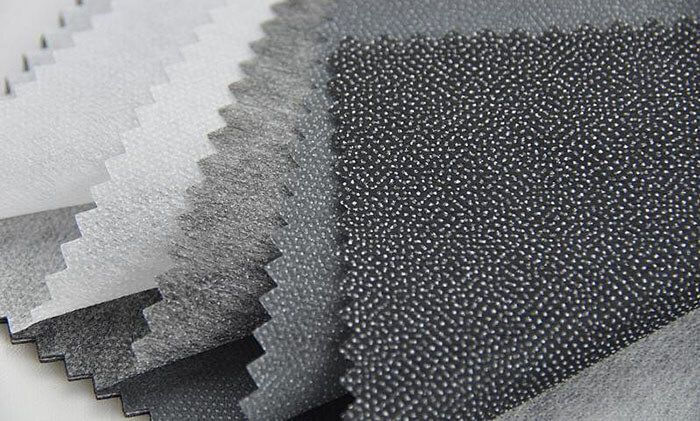
When working with non-woven interlining, proper preparation of both the interlining and fabric are crucial for achieving optimal results. This section will discuss important steps and techniques to follow when preparing the interlining and fabric before application.
1.) Pre-Shrinking the Interlining and Fabric: Before starting the application process, it is essential to pre-shrink both the non-woven interlining and the fabric to avoid any potential issues later on. Follow these steps for pre-shrinking
Interlining: Place the non-woven interlining in a basin or sink filled with warm water. Gently agitate the interlining for a few minutes, then rinse it thoroughly with cold water. Squeeze out the excess water and lay the interlining flat to air dry. Avoid wringing or twisting the interlining, as this can cause distortion.
Fabric: Different fabrics may require different pre-shrinking methods. Check the care instructions for your specific fabric and follow the recommended pre-shrinking process. This may involve washing the fabric in cold water or using steam to relax the fibers. Once pre-shrunk, press the fabric to remove any wrinkles.
2.) Selecting Appropriate Interlining and Fabric Combinations: The success of your project depends on choosing the right combination of fabric interlining. Consider the following factors when selecting your materials
Fabric Weight: Match the weight of the interlining to the weight of the fabric. A lightweight interlining suits lightweight fabrics, while heavier fabrics require a sturdier interlining for proper support and structure.
Fabric Composition: Consider the composition of the fabric, as some fabrics may be more compatible with certain types of interlining. For example, synthetic fabrics work well with polyester-based interlining, while natural fibers like cotton or silk may require a different type of interlining.
Garment Style: The style of the garment also influences the choice of interlining. For instance, a collar or cuff may require a stiffer interlining to achieve a crisp appearance, while a more flexible interlining may be suitable for a softer garment.
3.) Handling and Cutting the Interlining: When handling and cutting the non-woven interlining, it is essential to take precautions to ensure accurate and clean cuts
Use a rotary cutter or sharp scissors to cut the interlining. Avoid dull or serrated blades, which can cause fraying or uneven edges.
Place the interlining on a clean, flat surface, ensuring it lies smoothly without wrinkles or folds.
Mark the cutting lines on the interlining using fabric chalk or tailor's pencil. Double-check the measurements to ensure accuracy.
Cut the interlining along the marked lines, making clean and precise cuts. Take care to follow the grainline if applicable.
Once cut, handle the interlining gently to prevent distortion or stretching.
These preparation techniques will set a solid foundation for successful non-woven interlining applications. Pre-shrinking the interlining and fabric, selecting suitable combinations, and handling and cutting the interlining with care will contribute to achieving professional and durable results in your garment construction project.
Our Website Blogs
Our Document Download
Comentários