Common Challenges Faced by Elastic Webbing Manufacturers and How They Overcome Them
- stkinterliningseme
- Oct 5, 2024
- 6 min read
Elastic webbing is a versatile material used in various industries, including fashion, automotive, healthcare, and sportswear. It provides stretch, flexibility, and support, making products like waistbands, suspenders, athletic wear, and medical devices essential. The manufacturing of elastic webbing is a specialized process that involves blending different materials and precise control of tension, elasticity, and durability.
Like any manufacturing process, producing high-quality elastic webbing comes with its own set of challenges. These challenges can arise due to the complexity of materials used, the need for advanced technology, market fluctuations, and the ever-growing demand for sustainability. Manufacturers must ensure that their products meet stringent quality standards and adapt to the changing needs of consumers and industries. This blog will explore the common challenges elastic webbing manufacturers face and how they effectively overcome them.
Raw Material Selection and Sourcing

Challenge:
One of the fundamental challenges in manufacturing elastic webbing is selecting the right raw materials. Elastic webbing typically comprises rubber, polyester, nylon, spandex, or latex. The choice of materials is critical because it directly affects the product's stretchability, durability, and comfort.
Sourcing high-quality raw materials consistently is also a major concern. Fluctuations in the availability or price of these materials, especially natural rubber or latex, can disrupt production and lead to increased costs. Manufacturers must ensure the raw materials they use meet industry standards, are safe for consumers, and are sourced ethically and sustainably.
Solution:
Manufacturers overcome this challenge by establishing strong, long-term relationships with reliable suppliers who provide consistent, high-quality raw materials. Some manufacturers work with multiple suppliers to mitigate the risk of shortages or price hikes. Additionally, they invest in research and development to explore alternative materials that are more sustainable or cost-effective, such as synthetic elastomers or recycled fibers.
To address quality concerns, manufacturers often conduct thorough quality control checks at the sourcing stage, ensuring that all materials meet the required specifications before entering the production process. Manufacturers can also address the growing consumer demand for environmentally responsible products by adopting sustainable sourcing practices and eco-friendly materials.
Maintaining Consistent Elasticity and Tension
Challenge:
Achieving and maintaining the correct level of elasticity and tension in webbing is a significant challenge in production. Elasticity is crucial for ensuring that the webbing performs as intended, whether in clothing, automotive seat belts, or medical braces. Variations in tension can lead to inconsistent products that stretch too much or not enough, compromising their functionality and comfort.
Moreover, balancing elasticity with durability is difficult. Elastic materials can lose their stretchability over time, especially when exposed to heat, moisture, or repeated use. Ensuring long-lasting elasticity is a key concern for manufacturers.
Solution:
Manufacturers address this challenge by investing in advanced machinery that allows precise control over tension during the weaving or knitting. Modern equipment with digital monitoring systems can detect variations in tension and make real-time adjustments to ensure consistency. Additionally, manufacturers conduct regular quality assurance tests, such as stretch and recovery tests, to evaluate the performance of the webbing under various conditions.
For long-term durability, manufacturers use a combination of synthetic fibers like spandex or elastane, which offer superior stretch retention compared to natural rubber. Some companies also apply coatings or treatments to the webbing to improve its resistance to environmental factors like heat, UV rays, and moisture, helping to extend the product's life.
Ensuring Durability and Wear Resistance
Challenge:
Elastic webbing is used in products that undergo significant wear and tear, such as sportswear, luggage straps, and orthopedic devices. Manufacturers must ensure that the webbing can withstand repeated use without fraying, losing its elasticity, or degrading over time.
Elastic webbing is often exposed to harsh conditions, including stretching, friction, heat, sweat, and chemical exposure, all of which can deteriorate the material. For example, in medical applications, elastic webbing must maintain its strength and elasticity despite frequent washing and disinfecting, while automotive webbing must endure high temperatures and UV exposure.
Solution:
To enhance durability and wear resistance, manufacturers use high-quality synthetic fibers such as polyester or nylon, known for their strength and resistance to abrasion. Polyester, for example, has excellent moisture-wicking properties and is resistant to shrinking and stretching, making it ideal for elastic webbing used in high-performance applications.
Manufacturers also apply protective coatings or finishes to the webbing to improve its resistance to environmental factors. For example, UV-resistant coatings help prevent degradation from prolonged sun exposure, while moisture-resistant treatments protect the webbing from sweat, water, or chemical exposure. Regular testing, such as abrasion resistance tests, ensures that the webbing meets durability standards before it reaches the market.
Customization and Design Flexibility
Challenge:
Elastic webbing is used across various industries, each with specific requirements regarding design, stretch, width, color, and performance. For example, the automotive industry requires strong and durable webbing for seat belts. In contrast, the fashion industry demands lightweight, stretchy webbing that is available in a wide range of colors and patterns.
Meeting these diverse demands while maintaining high production efficiency can be challenging for manufacturers. Producing small, custom batches for different clients, each with its specifications, requires flexibility and can complicate the production process.
Solution:
Manufacturers overcome this challenge by offering high customization in their production processes. Many companies invest in advanced machinery that allows for quick changes between production runs, enabling them to produce custom batches with varying widths, colors, or elasticity.
Additionally, manufacturers use digital design and color-matching systems to ensure they can produce webbing in any shade or pattern requested by their clients. By offering a wide range of customization options, manufacturers can cater to the specific needs of different industries without sacrificing efficiency.
To maintain efficiency, manufacturers often create modular production systems that allow easy switching between different types of webbing. This flexibility is key to serving a diverse clientele without incurring excessive downtime or production delays.
Meeting Environmental and Regulatory Standards
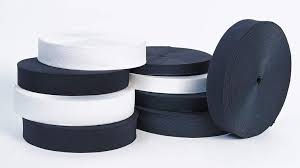
Challenge:
In recent years, manufacturers have been pressured to adopt sustainable practices and meet stricter environmental regulations. Elastic webbing production can be resource-intensive, using synthetic materials, chemicals, and significant energy. Additionally, many industries, such as automotive and medical, have stringent regulatory requirements regarding safety, toxicity, and material performance.
Manufacturers must balance the need for high-performance webbing with the demand for eco-friendly practices and compliance with industry regulations, which can vary from region to region and industry to industry.
Solution:
Elastic webbing manufacturers are increasingly adopting sustainable production practices to address these challenges. This includes using eco-friendly or recycled materials, reducing waste during the manufacturing process, and implementing energy-efficient technologies. Some manufacturers have begun to explore using bio-based elastomers as an alternative to traditional synthetic materials like rubber and spandex.
Compliance with environmental and safety regulations is also critical. Manufacturers ensure that their products meet industry-specific standards by working closely with regulatory bodies and obtaining certifications such as OEKO-TEX, which verifies that the materials used are free from harmful substances. Manufacturers can meet regulatory requirements by adopting sustainable practices and obtaining the necessary certifications while appealing to environmentally conscious consumers.
Managing Production Costs and Market Fluctuations
Challenge:
Like any manufacturing industry, elastic webbing manufacturers face the challenge of managing production costs, which can be affected by market fluctuations, raw material prices, labor costs, and global supply chain disruptions. Rising costs for key materials such as synthetic rubber, spandex, or polyester can lead to increased production expenses, which can be difficult to absorb in a competitive market.
Additionally, manufacturers must maintain competitive pricing while maintaining high quality, which can be difficult when operating in a global market where competitors may have access to cheaper resources or labor.
Solution:
Many manufacturers adopt lean manufacturing principles to manage production costs effectively. These principles focus on minimizing waste and optimizing production efficiency. Manufacturers can lower production costs without sacrificing quality by streamlining their operations and using advanced technology to reduce material waste.
In raw material price fluctuations, manufacturers often work with multiple suppliers to secure the best prices or negotiate long-term contracts that provide price stability. Additionally, some companies invest in automation to reduce labor costs and improve production efficiency.
Manufacturers that balance competitive pricing and high-quality products are better positioned to navigate market fluctuations and remain profitable even during challenging economic times.
Adapting to Technological Advances
Challenge:
The elastic webbing industry continually evolves, with new technologies and production methods emerging to improve efficiency and product quality. Keeping up with these advances can be challenging for manufacturers, especially smaller companies needing more resources to invest in the latest equipment or research and development.
Technological advances such as digital weaving machines, smart textiles, and 3D knitting can revolutionize the industry, offering greater precision, faster production times, and the ability to create more complex designs. However, adapting to these changes requires significant investment in equipment, training, and process development.
Solution:
Manufacturers that stay ahead of technological trends can gain a competitive advantage by investing in cutting-edge machinery and production techniques. For example, digital weaving machines allow more precise control over elasticity and tension, resulting in higher-quality products. Smart textiles, which integrate sensors and other electronic components, offer new opportunities for innovation in medical, sportswear, and automotive applications.
To manage the costs of adopting new technology, manufacturers may seek government grants or industry partnerships that support innovation and research. Training employees to operate new machinery and incorporating advanced technology into the production process ensures that manufacturers remain competitive in a rapidly changing industry.
The production of elastic webbing is a complex and specialized process that presents unique challenges. From sourcing high-quality raw materials to maintaining consistent elasticity, ensuring durability, and meeting regulatory standards, manufacturers must navigate numerous obstacles to produce high-quality products.
By investing in advanced machinery, adopting sustainable practices, and staying up to date with technological advances, elastic webbing manufacturer can overcome these challenges and continue providing versatile, reliable, and high-performance products across various industries. In a competitive and ever-evolving market, those manufacturers who can adapt to change and innovate will thrive, ensuring their products meet the demands of modern consumers and industries alike.
Comments